LatExpress
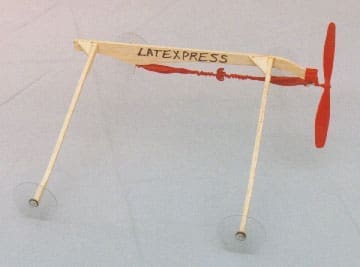
Race Order |
Entry # | Driver Name | Car Name | Mass (grams) |
Length (inches) |
Width (inches) |
Height (inches) |
Distance Traveled (feet) |
Running Time (seconds) |
27 | 46 | Mark Balzer | LatExpress | 25 | 12.5 | 15.75 | 5 | 12.75 | 1.80 |
Balloon car designer Mark Balzer writes:
- Design approach taken – explain how it worked.
Wound-up balloons were used, as in a rubber band powered airplane, to drive a propeller. The equal and opposite reaction force to pushing air backwards propelled the car forward.
I tied the two balloons together to make the rubber band as long as possible. One free end of the band was attached to the body of the car; the other end was attached to the propeller drive shaft (a bent piece of wire). The rubber band was twisted by winding the propeller in the reverse direction.
Some background… The most efficient way to store energy in a material is to stress the material in tension. I built the Dream Roller to use the balloon in uniaxial tension, like a rubber band, and wanted to do something different, quick and easy for a second car. Unfortunately, my “Faster, Better, Cheaper” car ended up taking much longer to build than the Dream Roller (because of its numerous intricate assemblies and belt sanded parts), and it didn’t go as far 🙁
From playing with rubber band powered airplanes as a child, I knew that a great deal of energy could be stored in a rubber band twisted in torsion. My initial thought was to build a car that used wound-up balloons as rubber bands to drive the wheels, using a miniature automotive design: the balloons would be the engine/transmission/driveshaft that turned the axle. The torque from the wound up balloons would then be delivered to the wheels which would push the car forward using friction between the road and tire. This turned out to be the design used by Paul MacNeal in his Rubber Fueled Dragster
The problem with this approach was that, since I started the night before the race, there was no time for me to get the right angle gearset and bearings needed to build the rear-axle unit.
Also, after the rubber band unwound and stopped powering the car, I wanted the car to be able to coast freely until its momentum was expended. This would have required a one-way clutch in the drivetrain.Therefore, at the expense of efficiency I decided to do the next best thing: use the torque from the wound up balloons to drive a propeller which propelled the car forward by pushing air backwards. The propeller drive also provides the coast feature without any extra effort.
- Unique or clever features embodied
The arms holding the wheels were reduced in cross-section to minimize weight and improve aerodynamics (air speeded up by the propeller but stopped by the car does you no good). The arms retained large cross sections at their ends to provide strong joints to the body and to the axles.
Shirt pins were used as 1″ long nails to attach the balsa wood arms to the body. Watered-down wood glue was then brushed over the joint and allowed to penetrate. Gussets were employed to stiffen the arms in the fore-aft direction. Gussets were also “nailed” in place. This resulted in extremely strong, moment-carrying joints that could take a lot of abuse.
The twisted rubber band/propeller drive generates two torques: one trying to rotate the propeller, and a counter-torque trying to rotate the body of the car in the opposite direction. (wind-up a wingless rubber band powered airplane and let go – you’ll quickly see what I mean 🙂 A wide track (width of the car) is needed to provide a large enough moment arm to allow the (low) weight of the car to supply the counter-torque needed to keep the propeller spinning counterclockwise (rather than the car spinning clockwise).
The hard plastic wheels provided a hard, narrow tread for low rolling resistance.
A Teflon (TM) disk was used on either side of each wheel to keep the wheel on the axle and minimize friction. The washer diameter was kept to a minimum to minimize parasitic drag torques.
The Teflon washer to plastic wheel interface was lubricated with powdered graphite to minimize friction.
Shirt pins were used as axles. They were stuck thru the Teflon disks and into the wooden arms to mount the wheels. This was quick and easy, plus allowed the freeplay in the wheel/axle assembly to be quickly adjusted by simply pushing the pin deeper into the wood.
A shirt pin was used to attach the balloon to the car body.
The body was made sculpted to clear the shape of the uninflated balloon so the balloon would not rub against the body as it untwisted.
The name LatExpress comes from Latex Express. The space and redundant letters were removed to save weight and stiffen the frame, er, uh, I mean, name.
- Materials of construction (mention unique parts you used or fabricated)
Balsa Wood
Shirt pins
Wood glue
Plastic “dish” hubcaps for an RC car (used as wheels)
Propeller and mount from a rubber band powered airplane kit - Reasons behind any significant design choices you had to make
I tried cutting the balloons down the middle and tying the halves together to make a band that was four balloons long, but the cut edge contained microscopic tears which, under tension, nucleated cracks that grew across the balloon half,
breaking it in two.I didn’t want to waste any balloon by tying it to the car body (any rubber in knots is rubber that can’t store energy to propel the drum), so I used a pin thru the balloon to hold it in place. It held perfectly, and allowed the balloons to be quickly and easily changed.
To allow the latex to slide over itself and prevent it from fusing (pressure welding) together when twisted tightly, I used liberal amounts of talcum powder, both inside and outside the balloons.
- Lessons learned (what you’d do differently next time)
These NASA guys are serious! Some of them spent 50+ hours working on their balloon cars!! I, on the other hand, was not planning on entering and only built this car the night before the race. My contest run was the first time I ever tried it outside! Next time, I will build earlier and do some testing on the course.
My balloon car zoomed off the line like a bat out of hell – its 5″ prop really got this lightweight car moving. Unfortunately, it made a left turn into the crowd, prematurely ending its run. This was probably due to the fact that the left wheels were more heavily loaded since they were carrying the forces used to generate the counter torque from the prop – so they had more rolling resistance than the right wheels.
If I had discovered the left turning problem (I would have seen it right away had I tested the car on the course), I would have redesigned (at least) one pair of wheels by attaching them rigidly to a solid axle. That would have forced a set of wheels to roll together and steer the car straight down the course.
- Anything else you’d like to add
The fastest “car” was a balloon powered airplane with essentially no mechanical modifications. (It minimized rolling resistance by leaving the ground, though it too veered off into the crowd.)
Even with its short run, the Latexpress was still the second fastest car… and the fastest one to stay on the ground! 🙂 Had I discovered and worked out the left turning problem, I believe the Latexpress would have been the fastest overall. Nevertheless, the fact that the two fastest cars were wound-up and propeller-driven proves the merit of this method of propulsion. Not a bad achievement for 4 hour’s work!
Despite their problems I had a lot of fun designing and building these cars, and must admit that I am quite proud of their (less than stellar) results. I think my cars need only minor tweaking to achieve their full potential.
MB 1/9/99