Dream Roller
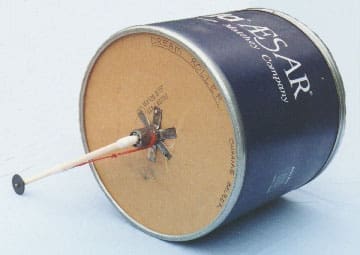
Race Order |
Entry # | Driver Name | Car Name | Mass (grams) |
Length (inches) |
Width (inches) |
Height (inches) |
Distance Traveled (feet) |
Running Time (seconds) |
Awards |
25 | 47 | Suzanne Balzer | Dream Roller | 3700 | 22 | 20.5 | 20.5 | 15.00 | 15.51 | Heaviest |
Balloon car designer Mark Balzer writes:
- Design approach taken – explain how it worked.
The most efficient way to store energy in a material is to stress the material in tension.
Rather than try to harness the bi-axial tension of the inflated balloon wall,
I decided to use the balloon in uniaxial tension, like a rubber band.
I tied the two balloons together to make the rubber band as long as possible.
The rubber band was tensioned by hand and wrapped many times, under tension, around a
cylindrical pulley which was attached to the bottom of a metal-edged, paper shipping drum.
The free end of the band was attached to a reaction arm. One end of this reaction arm was
mounted in a bearing attached to the drum; the other end held a wheel which rolled along
the ground behind the drum. The tensioned rubber band pulled against the reaction arm and
against the pulley. The rubber band and the geometry of the mechanism caused two torques
to be generated: one trying to rotate the reaction arm into the ground, and one in the
opposite direction trying to rotate the pulley attached to the drum. - Unique or clever features embodied
The metal edges on the drum provide a hard tread for low rolling resistance.
The wide track provided perfect steering. The Dream Roller went straight as an arrow.
The large diameter drum would not be affected by surface roughness of the concrete
course or small obstacles (pebbles, etc).After the rubber band unwound and stopped powering the drum, I wanted the drum to
be able to coast freely until its momentum was expended. I didn’t want the rubber band to start winding itself
up in the reverse direction and slow the drum down so I devised a way to disconnect
the rubber band just as it had given its all. I machined a keyhole slot into the pulley
into which the knot at the end of the tensioned balloon was inserted. The winding tension on
the balloon wedged the knot into the keyhole, holding it in place until the balloon had
unwound its last wrap on the pulley, at which point the pulley rotation moved the knot
to the opposite end of the keyhole, freeing it. The residual tension in the balloon then
pulled the balloon out of the keyhole, permitting the drum to roll freely.The name “Dream Roller” is a play on “Steam Roller.” I searched in vain for a better word than “dream” which rhymed with “steam” yet conveyed something about the motive power source. Sadly, engineers like myself don’t have much of a flair for poetry.
- Materials of construction (mention unique parts you used or fabricated)
Paper shipping drum with metal edges (lid removed)
Automobile exhaust adapter pipe, hack-sawed to create the spider-flange
Radial or “Conrad” type ball bearing
CPVC pipe and fittings
Model airplane wheel
Nuts and bolts - Reasons behind any significant design choices you had to make
I tried cutting the balloons down the middle and tying the halves together to
make a band that was four balloons long, but the cut edge contained microscopic tears
which, under tension, nucleated cracks that grew across the balloon half, breaking it in two.I didn’t want to waste any balloon by tying it to the reaction arm (any rubber in knots
is rubber that can’t store energy to propel the drum), so I used a tee fitting in the arm
to hold a short piece of pipe perpendicular to the arm. I slit this pipe with a hacksaw,
and wedged the balloon nozzle in the slit. It held perfectly, and allowed the balloons
to be quickly and easily changed.To allow the latex to slide over itself and prevent it from fusing (pressure welding)
together under the high stresses at the pulley, I used liberal amounts of talcum powder,
both inside and outside the balloons. - Lessons learned (what you’d do differently next time)
These NASA guys are serious! Some of them spent 50+ hours working on their balloon cars!!
I, on the other hand, was not planning on entering and only built this car the night
before the race from parts I had in my garage. My contest run was the first time I
ever tried it! Next time, I will build earlier and do some testing on the course.I should probably mention that I only came up with the Dream Roller design because my
original design was essentially disqualified on a technicality… I wanted to use the
two balloons to build a slingshot that would launch a projectile… an Estes model rocket
without the engine and chute… Unfortunately, according to Paul the contest organizer,
the “distance traveled” would have been zero, when measured at the slingshot 🙁(Hey Paul… so how come car 18, a slingshot design, is listed at 31.67 feet? 🙂
- Anything else you’d like to add
I was robbed!
I spent a lot of time on the mechanism that would allow the balloon to
disconnect from the pulley so the drum could roll freely, only to find that the uphill
course didn’t allow the drum to get up enough speed to make good use of this feature.
If the starting line and finish lines were reversed, This drum would have gone the whole
distance, and then some!The 15 foot mark was a wicked 1″ wide joint between the concrete slabs that made up the
course. The Dream Roller got stuck in that joint, ending my official run 🙁
However, when I ran up to the Dream Roller and moved it out of the joint, it started
rolling again under its own power and didn’t stop until it got to the 30 foot mark.
So at least in my mind, this heavyweight entry went 30 feet, uphill, using only
two balloons for power. The Dream Roller has the highest (Mass X Distance) product of
any entry, and that is one hell of an achievement for 4 hour’s work!
MB 1/9/99